- Like
- Digg
- Del
- Tumblr
- VKontakte
- Buffer
- Love This
- Odnoklassniki
- Meneame
- Blogger
- Amazon
- Yahoo Mail
- Gmail
- AOL
- Newsvine
- HackerNews
- Evernote
- MySpace
- Mail.ru
- Viadeo
- Line
- Comments
- Yummly
- SMS
- Viber
- Telegram
- Subscribe
- Skype
- Facebook Messenger
- Kakao
- LiveJournal
- Yammer
- Edgar
- Fintel
- Mix
- Instapaper
- Copy Link
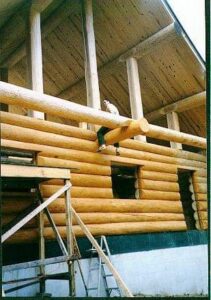
Randi’s husband at work on their house.
More than twenty years ago, my husband and I decided to build our own home and to make it as environmentally friendly as we could. We quickly found out that many different facets come into play when designing and building a home, especially ones that follow green building practices.
There are numerous decisions to make before the first shovel of dirt is moved. These include: the size of the home, the heating source, the water source, the septic or sewer system, and the main materials used for building the home. This essay takes a look at the selection of possible exterior building materials that people can chose in an effort to lower their carbon footprint when constructing their homes.
Of all the major building materials used in constructing a home, concrete is among the most carbon intensive. Concrete is made from Portland cement, water and aggregate. To produce cement, limestone must be heated to temperatures of 2400 degrees Fahrenheit. This requires enormous amounts of energy in the form of fossil fuels. Additionally, heating the limestone also releases carbon dioxide and calcium oxide.
According to a 2018 report by Chatham House, the concrete industry contributes about eight percent of the world’s global carbon dioxide emissions. The industry is currently researching ways to bring down these emissions in order to meet the Paris Accord, which will require a 16% reduction on their part. Unfortunately, global production of concrete is expected to increase over 5 billion metric tons per year over the next 30 years.
For this reason, avoiding concrete whenever possible is a better option. The website Homestratosphere.com offers a review of some of these options. Treated wood from designated tree farms can be used in some settings and the wood stores carbon. But a wood foundation can be difficult to maintain and requires using chemical treatment pre- and post-construction to avoid rot.
Many homes are built on a crawlspace foundation which cuts down on the amount of concrete needed while still providing access to plumbing, wiring, and duct work. The downside is that this offers little to no protection for homeowners during intense storms and can support the growth of mold and fungi. Granite foundations have been used in homes for centuries, but while they are durable and aesthetically pleasing, the granite must be quarried in an environmentally destructive process and transported from the site, further increasing the carbon footprint.
For the above grade portion of homes, concrete is not widely used, and there are less carbon intensive material options builders can choose to use. Most green choices are more expensive up front, but green building material options are becoming more popular and plentiful as people seek to lower their carbon footprint.
One of the oldest building materials used for construction is rammed earth. Originally, it was a mixture of clay rich soil, water, and a natural stabilizer such as animal urine, animal blood, plant fibers, or bitumen. The Great Wall of China is made of rammed earth. It’s easy to use and doesn’t require a lot of expertise.
However, rammed earth can be expensive, running about 250 dollars per a vertical square meter 30 cm thick. Also, the need for polystyrene insulation in walls and additional cement content to the earth mixture (for stabilization) adds to the carbon dioxide budget of the home.
The rammed earth technique is making a comeback. Today, the rammed earth design mixture has very optimum amounts of gravel, clay, sand, some cement or limestone, and some additives for waterproofing. If you can find the materials close to your building site, the transportation costs are negligible. The material is rammed between removable framework, usually plywood and can be rammed by hand or by machines.
The big pluses for this material according to the Australian Green Cross Project, include a four-hour-plus fire resistance rating and an ability to store heat and save energy. The downside, according to the site Treehugger.com, is that in many places like northern USA and Canada, the raw walls cannot withstand freeze-thaw cycles. This means an addition of cement (5 to 8 percent) to help with stabilization and this negates the environmental benefits. However, in some cases lime, blast-furnace slag or coal ash can be added to help with stabilization.
Another green building technique is straw bale construction. The first time I saw straw bale construction was in 1998 while taking a tour of a green college campus in Santa Fe, New Mexico. This technique has also been around for a very long time, including more than 100 years ago on Nebraska prairies. There is even a journal, The Last Straw, dedicated to educating people on this technique as well as other sustainable building practices.
Straw-bale construction was used in Germany more than 400 years ago. Homes can last more than 100 years and, according to a 2006 article in Mother Earth News, “homes made from straw bales are attractive, affordable, energy efficient and environmentally friendly.” They are extremely fire resistant. Research conducted by the National Research Council of Canada found that “bales withstood temperatures up to 1850 degrees for two hours.” Research has also shown that typical bales have an R-value of about 27.5. If you are close to a source of straw and do not require using excessive fossil fuels for transportation, these homes are very environmentally sustainable and affordable. The only downside is trying to convince lenders or insurers that your home is safe and sell-able and finding a way to work within building codes.
Ferrock is an iron-rich ferrous rock created from waste steel dust and silica from ground up glass. This material is the brain-child of Dr. David Stone. Dr. Stone patented the technique of using iron carbonate and is up to 95% recycled waste material. Dr. Stone came up with this product while completing his doctorate degree in Environmental Chemistry. With the help of a $200,000 EPA grant and the Southern Arizona O’odham Nation, Dr. Stone built a demonstration project using this material.
The major downside to the widespread use of ferrock, according to an article in Build Abroad, is that the use of the waste steel dust could become cost prohibitive if steel prices increase. The steel production process has a high carbon footprint which lessens the overall carbon-negative benefit of the ferrock production process.
According to Architectural Digest, bamboo may be one of the greenest building materials a homeowner can chose. The plant is a grass that can grow four feet a day. It doesn’t need to be replanted and is stronger than steel. It can sequester carbon dioxide from the atmosphere as it grows and in fact does this better than trees. It releases 35% more oxygen than trees as well. The Green Home Guide points out that bamboo is completely recyclable unlike a conventional home that generates 8,000 pounds of waste per 2,000 square foot home. It also is earthquake and hurricane resistant.
While bamboo is used in interior building materials for things like flooring, cabinets and interior walls, it can also be used for exterior construction. The downside of bamboo is that it must be shipped, usually long distances, from tropical regions. In addition, it can invade forests and destroy natural biodiversity.
Recycled plastic as a building material may seem like a win-win situation. The plastic decking and landscape materials used today come mainly from recycled plastic beverage bottles. The biggest advantage is that these materials will not rot or absorb water and they do not need to be stained and waterproofed like conventional lumber. They also harbor no toxic chemicals like pressure treated wood. Depending on the manufacturer, they can contain various percentages of recycled materials and can be made into composite with other components.
However, the Homebuilding Guide website points out that plastic cannot be used for structural applications as it lacks rigidity. While using recycled bottles does keep a percentage of plastic out of the environment, the product still relies on a petroleum-based polymer which has a high carbon footprint.
The National Hemp Association’s website contains an abundant amount of information on hempcrete. This material is a bio composite made from the inner woody core of a hemp plant mixed with a lime-based binder, sand and water. It is one-seventh the weight of concrete, is fire resistant, and can last 600-800 years. The silica in the hemp allows it to bind well with the lime. Advantages of hemp is that it requires no fertilizer to grow, no weed killer, pesticides or fungicides. As it grows it sequesters carbon dioxide in the same way that bamboo does, whereas concrete emits large amounts of carbon dioxide into the atmosphere.
It’s one downside is that it takes a very long time to cure and is not a good choice for load bearing walls. A way around this problem is being developed by using hempcrete block or bricks. After these blocks are cured, they can be used just like regular masonry blocks.
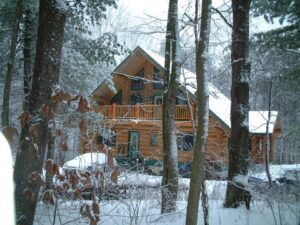
Randi’s house near completion.
We built our home over twenty years ago and while we tried to incorporate as many green building materials as possible, time and money often dictated our choices. Our outside structure is log walls. These came from a small company in British Columbia. While we acknowledge the carbon footprint for the transportation to Ohio, we console ourselves with the fact that except for the support beams in the second floor, all the logs came from forest fire-killed trees. These logs now sequester that carbon dioxide within our exterior walls.
Few building materials come without a downside environmentally speaking, but there are greener choices that are becoming more affordable each year.
Actually hempcrete cannot be used like bricks or concrete. It is not recommended for below grade due to moisture which can degrade hempcrete and it does not have compressive strength and therefore cannot be used structurally. But it can be used over frames and it’s fire resistant.